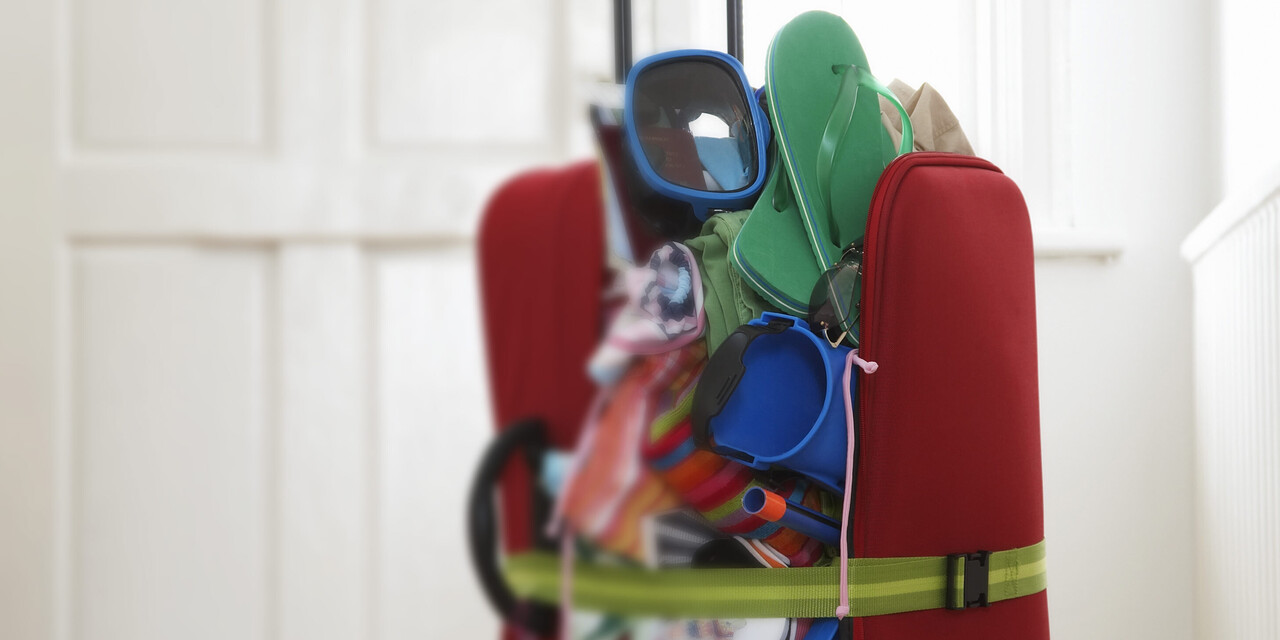
Effizienz in der Versandlogistik
Geschwindigkeit oder Sicherheit? In der Pack- und Versandlogistik ein alltägliches Spannungsfeld. Wie finden Unternehmen die richtigen Konzepte und den richtigen Kompromiss.
Geschwindigkeit oder Sicherheit? In der Pack- und Versandlogistik ein alltägliches Spannungsfeld. Wie finden Unternehmen die richtigen Konzepte und den richtigen Kompromiss.
Immer mehr Unternehmen richten ihr strategisches Navigationssystem auf Industrie 4.0 aus und setzen sich mit verheißungsvollen und zukunftsorientierten Themenfeldern wie Internet der Dinge, Big Data und 3D-Druck auseinander. Doch während derartige Ansätze eher langfristig orientiert sind, schlummert in den operativen Abläufen beträchtliches Effizienzpotenzial,das sich kurzfristig heben lässt. Zum Beispiel am Packplatz, der Schnittstelle zwischen Lager und Rampe.
Natürlich machen auch vor diesem Bereich moderne Technologien nicht halt – Stichwörter wie Robotik oder Augmented Reality sind hier nur einige Beispiele. Doch auch mit überschaubaren Mitteln und smartem Prozessdesign lassen sich beachtliche Optimierungen erreichen. Dabei sind die Anforderungen am Packplatz und im Versand hoch: Zum einen wollen die Unternehmen ihre Waren möglichst schnell, zum anderen auch in der richtigen Menge und Qualität versenden. In Anbetracht eines solchen Tempo-Sicherheits-Dilemmas müssen Unternehmen wirksame Konzepte entwickeln, die mal mehr in Richtung Zeitsparen, mal mehr in Richtung logistische Präzision tendieren können.
Welchem Aspekt größere Bedeutung beigemessen wird, hängt vom individuellen Umfeld des jeweiligen Unternehmens ab. Bei vielen Automobilzulieferern beispielsweise steht das Thema Sicherheit im Fokus. Sie sind darauf bedacht, die neuralgischen Punkte in der Logistik zu entschärfen, denn ein großer Automobilhersteller verzeiht in der Regel keine Fehler. Wer falsche Mengen oder Artikel liefert, nicht korrekt belabelt oder Packvorschriften nicht einhält, muss mit einer Rückstufung in der Lieferantenbewertung oder gar mit dem Verlust des Geschäfts rechnen.
Auch der Gasfedernhersteller Stabilus unterliegt als Zulieferer von namhaften Automobilherstellern strengen Richtlinien im Versand. Das Unternehmen hat daher eine Null-Fehler-Strategie implementiert. Ein wesentlicher Aspekt: die Doppelscannung, eine Extra-Sicherheitsstufe im Warenausgang. Hierbei scannt der Packer die Ware zum ersten Mal vor dem Ausdruck von Label und Lieferschein und ein zweites Mal, nachdem er das Label am Packstück angebracht hat. Das ist zwar zusätzlicher Aufwand und strenggenommen auch ein Zeitverlust. Aber nach den Worten von Stabilus-Versandleiter Berthold Wichterich lohnt sich die Doppelscannung für das Unternehmen: „Ein Kunde hat uns bestätigt, dass er noch nie ein so wasserfestes System gesehen hätte. Dieses Mehr an Qualität zahlt sich langfristig gesehen für uns aus.“
Allerdings bringt mehr Scannen nicht automatisch mehr Sicherheit, wie folgendes Beispiel zeigt: Ein Kunde hat 50 identische Exemplare eines Massenartikels bestellt, sagen wir eine Kaffeemaschine. Die Ware ist bereits kommissioniert und der Packer ist angehalten, jeden Artikel beim Einpacken zu scannen – 50 Mal die gleiche Identitätsprüfung, bei der gleichzeitig die Stückzahl kontrolliert wird. Das ist an und für sich ein verlässliches Instrument der Qualitätssicherung am Packplatz. Aber der Vorgang ist ebenso mühselig wie eintönig. Für den Packer ist in der Praxis die Versuchung groß, eine Kaffeemaschine in die Hand zu nehmen und deren Barcode 50 Mal einzuscannen. Anschließend verpackt er die kommissionierten Teile vorschriftsmäßig.
So ein Vorgehen klingt nachvollziehbar und effizient, aber leider bietet es keine Sicherheit, dass tatsächlich 50 Stück auf der Palette gelandet sind. Was ist, wenn der Kommissionierer zwei Exemplare vergessen hat? Dann bestätigt der Packer durch das fünfzigmalige Scannen des gleichen Labels lediglich die vorgegebene Anzahl, tatsächlich erreichen den Kunden nur 48 Stück – zuzüglich Reklamationsgrund und Ärgernis. Vermeiden lassen sich derartige Fehler, indem identische Artikel eine zusätzliche fortlaufende Nummerierung auf dem Barcodelabel erhalten. Dann kann jedes Exemplar beim Verpacken nur ein einziges Mal gescannt werden, jeder weitere Scanversuch löst im Versand- oder Lagerverwaltungssystem eine Fehlermeldung aus.
Um doppeltes Scannen und Zählen und somit personalintensive Redundanzen zu vermeiden, fassen manche Unternehmen das Kommissionieren und Packen in einem Prozess zusammen. Beim sogenannten Pick & Pack-Verfahren gibt das Warehouse Management System von vornherein vor, in welches Packmittel die Artikel gehören. Dann kommissioniert der Mitarbeiter in eine entsprechend dimensionierte Kommissionierkiste, deren Inhalt er am Packplatz nur noch in den Versandkarton „umschütten“ muss. Der Vorteil dieses Verfahrens: Da Picken und Packen in einem Arbeitsgang erfolgen, erübrigt sich das Nachzählen der Artikel am Packplatz. Der Nachteil: Die Fehleranfälligkeit ist deutlich höher. Das Verfahren kommt daher in der Regel eher bei kleineren Bestellungen zum Einsatz.
Immer größere Relevanz am Packplatz gewinnt das Thema Labeling. Die Basisarbeit besteht darin, das Frachtstück mit dem Label des jeweiligen Spediteurs oder Kurier-, Express- und Paket- kurz KEP-Dienstleisters zu versehen. Hört sich einfach an, ist es aber oftmals nicht. Denn jeder Transportdienstleister stellt ganz individuelle Anforderungen an Inhalte und Format. Die Label können auch komplexe Elemente wie beispielsweise Grafiken, inverse Felder oder (2D-)Barcodes enthalten. Fehlerhafte Label verhindern die termingenaue Beförderung und das Nachlabeln im Depot kann mit Zusatzkosten verbunden sein. Zwar bieten die größeren Dienstleister in der Regel eigene Softwarelösungen für den Druck der Versandetiketten. Jeder Spediteur und KEP-Dienst muss dann aber einzeln über jeweils eine separate Schnittstelle angebunden werden. Der Aufwand, diese individuell zu programmieren, abzustimmen und zu warten, ist hoch. Damit wird auch der Wechsel eines Transporteurs zeitintensiv, arbeits- und kostenintensiv.
Arbeiten Unternehmen mit mehreren KEP-Diensten oder Speditionen zusammen, ist es oftmals sinnvoll, diese mittels spezieller, übergreifender IT-Lösungen in die Versandprozesse zu integrieren. Derartige Software erstellt Routinglabel gemäß der Spezifikation des jeweiligen Dienstleisters. Das Layout kann bei Bedarf an individuelle Wünsche angepasst werden, sofern es der Dienstleister akzeptiert. Es können zum Beispiel zusätzliche, individuelle Angaben eingefügt werden. Darüber hinaus erstellen und übertragen die Softwarelösungen die notwendigen Dokumente und EDI-Nachrichten(Electronic Data Interchange) wie eine entsprechende Ladeliste.
Komplexer wird es, wenn Kunden spezifische Anforderungen an das Labeling stellen – also beispielsweise vorgeben, an welcher Stelle die Labels anzubringen sind. Daraus resultiert für die Packer spätestens dann eine knifflige Aufgabe, wenn der Kunde Hunderte verschiedene Lademittel vorschreibt. Bei der einen Kiste gehört das Label rechts oben auf den Deckel, bei der anderen mittig auf die schmale Seitenfläche, für die dritte, vierte und fünfte Kiste gelten wieder andere Vorgaben. Wie also können Unternehmen ihre Mitarbeiter an der Packstraße unterstützen, damit sie Kartons, Kisten und Paletten richtig belabeln?
Ein probates Mittel sind Grafiken, schematische Darstellungen oder Fotos, die Anweisungen in Schriftform überflüssig machen. „So muss der Packer keine langen Texte lesen und weiß sofort, was zu tun ist“, lobt Stabilus-Logistiker Wichterich die Vorzüge der bildlichen Vorgaben. Auch bei der Vorbereitung von Gefahrguttransporten tragen eindeutige Abbildungen dazu bei, dass die Packer immer den im konkreten Einzelfall geforderten Warnhinweis auf dem Lademittel anbringen.
Ein gut funktionierender Packplatz kann entscheidend zur Kundenzufriedenheit beitragen. Dabei hilft nicht nur eine hohe Lieferqualität. Auch durch spezielle Mehrwertservices beweist der Versender seine Kundennähe. Wie dies aussehen kann, zeigt Epcos, ein führender Hersteller von elektronischen Bauelementen wie Kondensatoren und Sensoren. „Nur wenn die Pick- und Packprozesse reibungslos verlaufen, können wir knappe Lieferfristen und spezifische Kundenanforderungen einhalten“, bestätigt Gerhard Hofmann, Manager Information Technology and Logistics der Epcos AG.
Bestellt ein Kunde beispielsweise 1.000 Kondensatoren, so kann dieser Artikel beim Kunden für unterschiedliche Produkte und damit auch Produktionsprozesse eingeplant sein. Das bedeutet, dass die Versandposition zum Beispiel aus zehn unterschiedlichen Produktverpackungen mit jeweils 100 Stück des gleichen Kondensators bestehen kann. Jede dieser zehn Produktverpackungen bekommt vom Versandsystem jeweils andere Labels, etwa mit einer spezifischen Kunden-Serien-Nummer. Auf diese Weise kann der Kunde von Epcos die Kondensatoren direkt in seine Produktionsprozesse einsteuern.
Um derartige Kundenanforderungen zu erfüllen, sind bei Epcos in der Versandsoftware bis zu 900 unterschiedliche Labels zu finden. Für diese ist ein komplexes Regelwerk hinterlegt, das automatisiert vorgibt, welche Labels in welchem Prozess wie oft gedruckt und wo angebracht werden müssen. Zudem können innerhalb weniger Stunden auch neue spezifische Kunden-Labels erstellt und nach Freigabe durch den Kunden zentral an alle Standorte weltweit verteilt werden.
Ein weiterer Optimierungsfaktor am Packplatz ist das Packen in die Versandverpackung. Der Clou dabei ist die automatische Konsolidierung von Bestellungen, um Versandkosten zu sparen: Die Software stößt automatisch eine Beipackbildung an. Hat ein Kunde mehrere Bestellungen aufgegeben, werden diese nach Möglichkeit auf Lieferscheinebene verlinkt und der Mitarbeiter kann diese zusammen in einem Versandkarton verpacken.
Fragt sich noch, wie man die Nachschubversorgung am Packplatz steuert, damit bei den Mitarbeitern kein Leerlauf entsteht. Die meisten Unternehmen verfolgen dazu das altbewährte Push-Prinzip: Die Kommissionierer arbeiten einen Auftrag nach dem anderen ab und schieben („push“) die Waren in Richtung Packplatz. Nicht selten kommt es dort zu Rückstaus, wenn zu viele Artikel die Regale frühzeitig verlassen haben. Das Ergebnis:Ware, die platzraubend herumsteht und die Abläufe im Lager behindert. Eine Möglichkeit für spürbare Entspannung: der Wechsel vom Push- zum Pull-Prinzip. Hier sind es die Packer selbst, die den nächsten Kommissioniervorgang veranlassen und somit im übertragenen Sinne die Ware zum Packplatz ziehen („pull“). Genauer gesagt ist es das Warehouse Management System, das die Dauer der einzelnen Packvorgänge auf Basis von Erfahrungswerten abschätzt und erst dann die nächste Kommissionierung auslöst, wenn der Packplatz Nachschub verträgt.
Ein weiteres Erfolgsrezept, um Platz für effiziente Prozesse am Packplatz zu schaffen, ist die Einrichtung von Projektpackplätzen für Großaufträge. Wie dies aussehen kann, zeigt der Medizintechnik-Hersteller Aesculap. In dem Tuttlinger Unternehmen müssen die Packer Bestellungen mit bis zu 10.000 Auftragszeilen abarbeiten. Wenn sie für eine einzelne Klinik 5.000 verschiedene Instrumente zu 200 Einzellieferungen zusammenstellen, haben sie weder den Kopf noch die Fläche frei, um nebenbei eine Handvoll Skalpelle für eine Apotheke einzupacken. Deshalb weist Aesculap für „Riesenpakete“ einen separaten Arbeitsplatz aus, der vom restlichen Treiben im Warenausgang abgeschirmt ist. Auch für die Vorbereitung von extra großen und extra schweren Packstücken hält Aesculap im eigenen Logistikzentrum ausreichend Platz frei.
Die Beispiele zeigen: Durch smarte Konzepte und Prozessoptimierung lassen sich Schnelligkeit und Sicherheit am Packplatz und im Versand weiter steigern. Voraussetzung dafür ist eine leistungsfähige und flexible Softwareunterstützung, die in die gesamte IT Landschaft des Unternehmens integriert sein sollte. Sie hilft beispielsweise bei der Auswahl des Packmittels ebenso wie bei der Entscheidung für den geeigneten Transportdienstleister. Entsprechend spezialisierte Lösungen sind heute bereits am Markt verfügbar.
Nachholbedarf gibt es dagegen bei der Automatisierung. Daher setzt Berater John A. Eke auf den gesunden Mittelweg zwischen digitaler Unterstützung und menschlichem Beitrag: „Von Versand 4.0 sprechen wir noch lange nicht. In diesem Bereich ist die Automatisierung längst nicht so ausgereift wie bei der Regal- und Kommissioniertechnik. Wer auf Nummer sicher gehen will, der leistet sich an jeder Packstraße auch qualifizierte Kräfte, die Augenmaß und Erfahrung einbringen“, rät der geschäftsführende Gesellschafter von Exxent Consulting. Am besten verlasse man sich nicht ausschließlich auf ständig wechselnde Leiharbeiter, sondern auf eigene Leute, die sich mit den Produkten auskennen. „Wer im Warenausgang allein ungelernte Hilfskräfte beschäftigt, darf sich nicht wundern, wenn seine Produkte in der falschen Verpackung oder in zu vielen Einzelpaketen auf die Reise gehen“, sagt Eke. Im ersten Fall ärgert man sich über hohe Transportschäden, im zweiten über hohe Transportkosten.