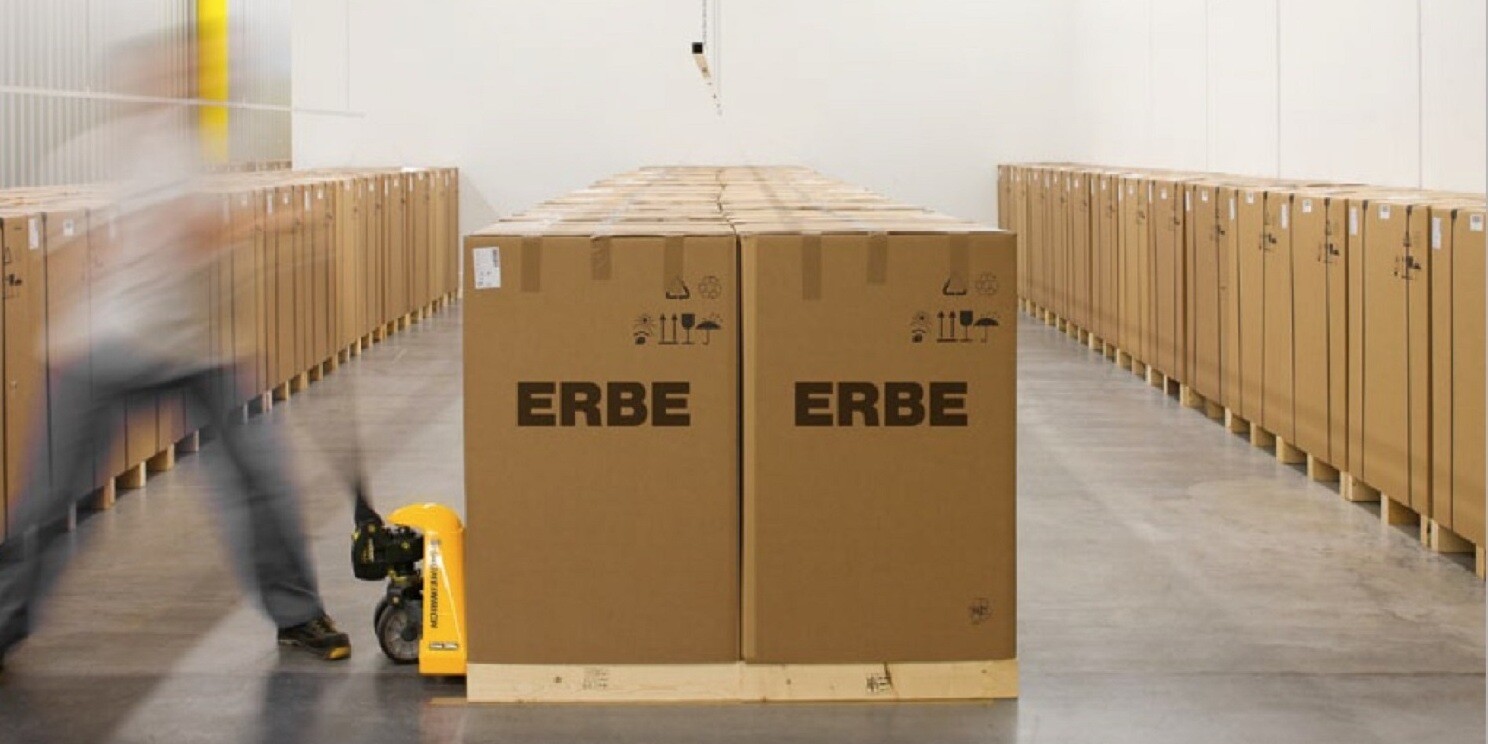
Besser Kommissionieren mit einem Lagerverwaltungssystem von AEB
Case Study: ERBE Elektromedizin steigert mit AEB Lagerverwaltungssystem Effizienz der Intralogistik – vom Wareneingang über Kommissionieren bis hin zum Versand.
Case Study: ERBE Elektromedizin steigert mit AEB Lagerverwaltungssystem Effizienz der Intralogistik – vom Wareneingang über Kommissionieren bis hin zum Versand.
Die ERBE Elektromedizin GmbH produziert medizinische Geräte in Tübingen und versendet jährlich rund 60.000 Sendungen mit Geräten und Zubehör an Krankenhäuser, Arztpraxen und autorisierte Händler. Der Exportanteil liegt dabei bei über 80 %.
Die Hälfte des Sendungsvolumens besteht aus großen Sendungen mit medizinischen Geräten und Instrumenten. Kleinere Sendungen mit Zubehör wie Mikropinzetten oder Sonden für die Endoskopie machen den anderen Teil aus, wobei dieser Anteil stetig zunimmt.
Mit AEB Warehouse Management - dem Lagerverwaltungssystem für höhere Performance in Ihrer Lagerlogistik.
Im Jahr 2005 fasste ERBE den Entschluss, die Lagerhaltung europaweit zu zentralisieren und ein neues Distributionscenter in Tübingen zu bauen. Das 3.000 qm große, hochmoderne Logistikzentrum wurde 2008 eröffnet und umfasst sechs Lagerbereiche:
Michael Ankele, Leiter Materialflusswirtschaft: „Wir profitieren heute von kurzen Wegen und können den Produktionsnachschub eng mit dem Lagernachschub verknüpfen. Die Logistik ist jetzt direkt an unsere Produktionsprozesse angebunden, was wertvolle Synergieeffekte schafft.“
Vor dem Bezug des neuen Logistikzentrums war die logistische Abwicklung von manuellen Abläufen geprägt. Zusätzlich zu neuen gesetzlichen Anforderungen – Teilnahme am elektronischen Ausfuhrverfahren, Einhaltung von Compliance-Regeln und Antiterrorverordnungen der EU – gab dies den Anstoß, sich nach einer Software zur Unterstützung der Versand- und Exportprozesse umzusehen. Gleichzeitig musste ein Lagerverwaltungssystem gefunden werden.
Ausschlaggebend für die Entscheidung zugunsten der AEB war die Aussicht darauf, ein Versand- und Exportsystem sowie ein Lagerverwaltungssystem aus einer Hand zu erhalten. Die Versandabwicklung sollte IT-gestützt erfolgen, um für zukünftige Aufgaben gerüstet zu sein.
Michael Ankele: „Wir haben erkannt, dass unser ERP-System nicht so weit ausbaufähig ist, dass damit das zukünftige Lager in unserem Sinne verwaltet werden konnte. So standen wir vor der Wahl: zwei separate Spezialisten zu finden oder einen Anbieter, der beides kann.“ IT-Leiter Wolfgang Werz äußerte den Wunsch, möglichst einen Anbieter zu wählen, um das Problem der Anbindung und Schnittstellen zu umgehen.
„Als erstes wurde die AEB Software für die Bereiche Versand, Export, Import, Compliance und Fracht implementiert. Als die Mitarbeiter dann mit der Software vertraut waren, wurde zusätzlich das Lagerverwaltungssystem angedockt“, erzählt Paul Rivera, der das Projekt auf AEB-Seite leitete.
Der gesamte intralogistische Prozess vom Wareneingang, dem Picken und Kommissionieren, über das Verpacken und Bereitstellen aller Frachtdokumente bis hin zum Warenausgang wird nun systemseitig abgebildet und das Lagerverwaltungssystem führt die Mitarbeiter durch ihre Aufgaben.
Maßgeblich bei der Planung und Gestaltung der IT-technischen Abbildung der neuen Logistikabwicklung waren Standardisierung und Automatisierung. ERBE versteht die Automatisierung auch als prozesstechnische Unterstützung.
Michael Ankele sieht als großen Gewinn des Lagerverwaltungssystems die Geradlinigkeit der Prozesse: „Die Aufgabe der Software war es dabei eher, das umzusetzen, was gedanklich schon in unseren Köpfen war, nämlich die Durchgängigkeit der Prozesse.“ Die Prozessunterstützung stellt das Lagerverwaltungssystem sicher durch:
Im Wareneingang sorgt das Lagerverwaltungssystem von AEB dafür, dass die eingehenden Waren zielgerichtet in die zuvor anhand von Einlagerungsstrategien festgelegten Lagerplätze geroutet werden.
Sobald die Auftragsdaten vom ERP-System an das Lagerverwaltungssystem von AEB übergeben wurden, generiert dieses Sendungen und Auslagerungsaufträge, reserviert die Ware im betreffenden Lagerbereich und berechnet automatisch die Wege der Mitarbeiter zum Kommissionieren und der Ware durch das Lager.
Gibt der Mitarbeiter beim Kommissionieren am AKL den Anstoß zur Auslagerung, generiert das Lagerverwaltungssystem die Fahrbefehle. Der Materialflussrechner steuert den Transport des jeweiligen Tablars an einen der Plätze zum Kommissionieren. Ein Laserstrahl richtet sich auf das Tablarsegment, aus dem die Ware zu kommissionieren ist, und eine grafische Anzeige auf dem Monitor markiert das richtige Fach.
Um Fehler beim Kommissionieren zu vermeiden, scannt der Mitarbeiter zuerst den Behälter, aus dem die Ware zu kommissionieren ist, dann den zu entnehmenden Artikel. Schließlich scannt er die Handling Unit, in die der Artikel nach dem Kommissionieren für den weiteren Transport zum Packplatz gelegt wird.
Auch Kommissionieren im Hochregal-Palettenlager wird von dem Lagerverwaltungssystem unterstützt. Das Lagerverwaltungssystem berechnet stets die beste Route innerhalb des Lagers anhand in den Stammdaten hinterlegter Transportketten und Prioritäten.
Während dem Mitarbeiter im Hochregallager die wegeoptimierten Fahraufträge durch das Leitterminal im Gabelstapler angezeigt werden, erfüllt in den übrigen Lagerbereichen ein Handheld diese Aufgabe. Die Entnahme der Ware erfolgt in allen Lagerbereichen scannergestützt.
Nach dem Kommissionieren wird die Ware dann an dem ursprünglich für diese Sendung definierten Konsolidierungsfach oder -linie bereitgestellt. Der Mitarbeiter wird auf dem Handheld der Konsolidierungsplatz der Sendung angezeigt. Das Sendungsvolumen und -gewicht bestimmt, ob die Ware ins Durchlaufregal oder an eine der zehn Linien gebracht werden muss.
Das in den Produktionsprozessen eingeführte Pull-Prinzip wird nun auch auf die Logistik übertragen. Hierzu wurden so genannte „saugende Packplätze“ installiert und durch das Lagerverwaltungssystem abgebildet.
Engpässe werden dadurch vermieden, dass ein Auftrag zum Kommissionieren erst dann ausgelöst wird, wenn eine Linie oder ein Platz im Durchlaufregal entsprechende Kapazität aufweist. Das Lagerverwaltungssystem registriert, wie viele der Übergaberegale belegt sind. Sobald ein Fach frei ist, ordnet es automatisch einen neuen Lagerauftrag zu.
Nach der systemgestützten Überprüfung auf Vollständigkeit gibt das Lagerverwaltungssystem die jeweilige Sendung zur Verpackung frei. Dem Packer wird dies durch entsprechende Kennzeichnung in der Packplatz-Anwendung des Lagerverwaltungssystems signalisiert.
Der Verpackungsprozess erfolgt „qualifiziert“: Jeder Artikel mit Chargen- bzw. Seriennummer wird vor dem physischen Verpacken per Scan nochmals auf Sendungszugehörigkeit überprüft. Dies vermeidet nicht nur einzelverrichtungsbezogene Fehler und unterstützt damit die Null-Fehler-Strategie im Gesamtsystem. Es trägt auch zur chargen- und seriennummernbezogenen Rückverfolgbarkeit bei.
Wie die übrigen sendungsbezogenen Dokumente wird auch die Packstückliste im Prozess durch das System generiert, im Versandbüro gedruckt und kontrolliert und kann nach Abschluss der Verpackung zeitnah der Sendung beigelegt werden.
Nicht nur die Lagerarbeiter werden bei ihren Aufgaben von der Software unterstützt, auch der Lagerleiter hat die Prozesse, die er zu verantworten hat, stets im Blick. Im so genannten Lager-Cockpit findet er Informationen über die Anzahl offener Transportaufträge und eine Übersicht der Lageraufträge insgesamt.
Er sieht, welche Sendung schon wie lange im Durchlaufregal steht. Ampelanzeigen signalisieren, wenn es Verzögerungen gibt. Zudem hat er Zugriff auf Auswertungen und kann Statistiken erstellen. Gab es vor der Einführung der AEB-Software keine Auswertungsmöglichkeiten, so kann heute einfach ermittelt werden, wie viele Sendungen in welches Land versendet wurden, mit welchem Spediteur, mit welchem Gewicht etc.
Ankele begrüßt diese Auswertungs- und Steuerungsmöglichkeiten: „Wir haben dadurch sehr viel mehr Prozesssicherheit gewonnen. Fehler werden schneller entdeckt und ausgeräumt – das schafft stabile Prozesse.“
2012 führte Erbe auch AEBs Software Monitoring & Alerting ein. Die Erbe-Mitarbeiter am Stammsitz und in den weltweiten Tochtergesellschaften erkennen mit Hilfe der Online-Anwendung auf einen Blick, welchen Status eine Sendung hat.
Die Erbe-Tochterunternehmen in Belgien oder in den USA können selbst ihre Aufträge aufrufen. Sie sehen, ob die Ware noch beim Kommissionieren ist oder „verpackt“ wurde oder der Warenausgang erfolgt ist. Die Statusmeldungen der Transportdienstleister, die mit Erbe zusammenarbeiten, z. B. DHL, FedEx, Kühne + Nagel und Transmed, werden ebenfalls eingespielt. Auch diese Informationen sind in Echtzeit verfügbar.
Nicht nur der Warenempfänger kann sich nun selbst informieren, auch der Logistikleiter selbst erhält die wichtigsten Informationen zur Performance auf einen Blick. Mit dem „Performance-Indikator“ kann sich der Logistikleiter jederzeit darüber informieren, wie viele Sendungen in einem definierten Zeitraum verschickt wurden und wie viel Prozent der Sendungen im Zeitplan waren.
Den Logistik-Verantwortlichen bei Erbe ging es darum, den Warenfluss sowohl im Haus als auch zum Kunden hin transparent zu gestalten und Verzögerungen frühzeitig entgegenwirken zu können. Anhand der Visibility-Software lässt sich nun sehr schnell feststellen, wenn Ware zu lange in einem Hub liegt oder sich eine Verzögerung in der Auslieferung anbahnt.
Mit Hilfe der IT kann nun die Einweisung der auf direktem Weg an die europaweiten Kunden gelieferten Waren terminiert und geplant werden. Erbe kann bei Zwischenfällen rechtzeitig reagieren und so Verzögerungen vermeiden. Insgesamt profitieren heute sowohl Erbe als auch die Kunden von durchgängigen transparenten Prozessen bis zur Anlieferung am Bestimmungsort.
Das integrierte Compliance-Screening gleicht automatisiert alle Liefer- und Rechnungsempfänger mit den Sanktionslisten der EU und USA ab und stellt sicher, dass keine Sendung an Terrorverdächtige ausgeliefert wird.
„Auch wenn sich alle vermeintlichen Treffer bisher als Namensgleichheiten – und damit als Fehlalarm – herausgestellt haben, ist es einfach wichtig, diese Vorgänge zu protokollieren, um im Falle einer Überprüfung durch die Zollbehörden auf der sicheren Seite zu sein“, erläutert Michael Ankele.
Das Investitionsvolumen für den Bau des Lagers und der Einführung des Lagerverwaltungssystems und der Versandsoftware betrug rund acht Millionen Euro. „Die logistischen Abläufe sind heute weniger individuell geprägt, aber dafür dank der durchgängigen Systemunterstützung sicherer und effizienter“, so das Fazit des Projektleiters Ankele.
Die Einführung des Lagerverwaltungssystems sorgte dafür, dass weniger Leute mehr Sendungen bearbeiten können. „Heute bewältigen wir sehr viel mehr als früher mit unserer Stammmannschaft und haben noch Potenzial für zukünftige Entwicklungen“, äußert sich Ankele zufrieden.
Die ERBE Elektromedizin GmbH, einer der führenden Anbieter auf dem Weltmarkt für medizinische Geräte, entwickelt innovative Geräte für die Hochfrequenz-Chirurgie, die Wasserstrahlchirurgie sowie Instrumente und Zubehör für Blutstillung, Tumorentfernung und minimalinvasive Operationen. Das Unternehmen hat Niederlassungen und Tochterfirmen in elf Ländern: Frankreich, Großbritannien, Holland, Belgien, Österreich, Schweiz, Polen, Russland, USA, China und Indien.