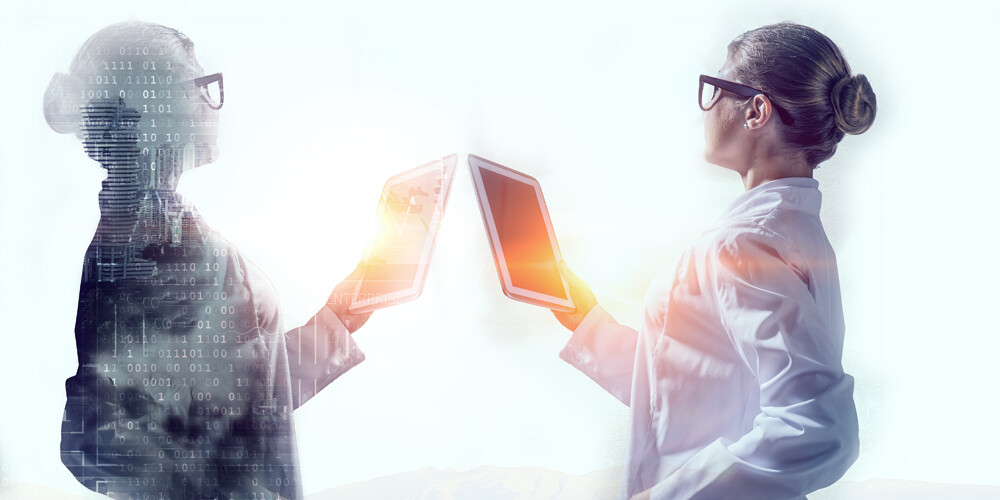
Sometimes good things come in pairs: The digital twin
What’s a digital twin? How is it used – in private life, manufacturing, farming, or warehousing? Find out what the relevance is for supply chain management.
What’s a digital twin? How is it used – in private life, manufacturing, farming, or warehousing? Find out what the relevance is for supply chain management.
Today I’d like to take a closer look at the “digital twin” – and what it’s all about. It’s not really a new term – it was already introduced back in 2001 by Dr. Michael Grieves. The term has strongly evolved over time from its original focus on product design. Google currently records more than 3 million queries – per second(!). This volume qualifies it as a hype but whether everyone means and understands it the same, is another matter altogether. In manufacturing, particularly around machinery and plant engineering, the digital twin has become part of the standard repertoire by now. In my view, it’s also of high relevance for supply chain management.
A picture that always comes to (my) mind when contemplating the concept of the digital twin is a photograph showing Albert Einstein with his twin brother. The brother, after returning home from space travel, surprisingly has barely aged. Einstein’s very own theory of relativity delivers the reason for this phenomenon. However, the asymmetry of space-time paths from this thought experiment is not easy to understand.
So, even though this comes to mind straight away, the Einstein example leads us down a wrong path. Why? Because the symmetry of the image is a crucial aspect for the digital twin. Based on models, classifying data, and environmental information, every real object can be recorded with characteristics, condition, or behavior. In fact, this also applies to every service and all intangible goods. Already today, many products carry along with them a more or less pronounced “digital shadow” based on operational data, process data, and status data.
A digital twin is created by combining a unique instance of a universal digital template (description, control, and simulation model) and its digital shadow. Basically, we are dealing with twins that exist in different worlds. One in the real world and another in the virtual world. And the latter is exclusively there for the first – one could say to optimize its real existence.
Are you also well on the way to developing a “smart home fetish”? I’m completely fascinated by the options to monitor, control, and automate various things at home. My heating, for example, delivers a daily health check or reports to the installer if there is a problem. I’m always aware of the current room temperature, the corresponding progress curve of each thermostat, the condition of each smoke detector, and whether windows are tilted or not. I can influence many things directly or control timer settings. The systems detect if someone is home or not – and run respective profiles accordingly.
For every smart device, there is a digital instance – usually in the provider’s cloud. Continuously collected information is recorded there and (hopefully) evaluated for a specific purpose. The intelligence the control is based on is only partly integrated in the device itself – the main part is linked to a digital template that can easily be updated and further developed. This is how a digital twin of a heating thermostat learns to regulate and adjust temperature levels in line with outside temperature, weather forecast, and required deltas to reach its target.
From smart homes, let’s jump straight to devices in logistics: the intermodal shipping container. It was launched more than 60 years ago by the American freight forwarder Malcolm McLean. At the time, McLean’s main driver was the practical transfer from trucks to vessels. He hardly could have foreseen the resounding success of his invention for globalization. And even in his wildest dreams he probably never would have thought that one day communication with these boxes would be possible.
With its digital twin, a container is represented in the Internet of Things (IoT) and becomes a responsive object. It readily delivers information about current location, temperature, cargo, load level, weight, or its shipping route – if the entity that requests the information has the required access rights. At the same time, all data is also recorded to provide a seamless picture of the complete lifecycle. This enables, for example, options for deployment optimization, control of service levels, or functional forecasts.
Much more exciting, however, are the additional communication options. Especially, if they are made available to as many parties as possible. This can include, for example, checking the container’s calendar, viewing booked routes, and making new reservations in line with availability. The container is also aware of its cost profile and can provide quotations accordingly. Or the other way round: the container can pro-actively offer free capacities, increasing its economic efficiency through optimal market positioning for lucrative routes and/or offering discounts for return shipments.
Another example demonstrates the development potential of intelligent and connected machines very well: in agriculture, the farm tractor has evolved to become an integrated part of a system platform – thanks to sensor technology, actuator engineering, and internet connection. As a result, we can actually talk about an expansion and a new orientation of an entire industry branch. Take a look at this illustration for the evolutionary steps from the tractor’s original state to what it has become today.
For comparison with a more complicated object, let’s look at a warehouse system with respective material handling automation components. Its virtual image is pieced together by many digital representations of individual, technical components. But on the highest level of aggregation, data is condensed to supply the superordinate process control. The broad spectrum of deployment takes effect long before goods get stored – through digital planning and simulation tools.
Processes and equipment flow rates can be simulated already at the planning stage. Different configuration scenarios enable assessments of product extensions or gauge the impacts of product changes on operations. The virtual operation prevents downtimes during actual implementation and noticeably reduces problems in the initial go-live phase. During running operations, the digital twin monitors compliance with KPIs, identifies process weaknesses, and controls business contingency plans in case of equipment failures or other unexpected discrepancies.
The warehouse example brings us back to the area of plant engineering where, as mentioned earlier, the digital twin has achieved high relevance some time ago already. John Vickers, NASA’s leading manufacturing expert and manager of the NASA National Center for Advanced Manufacturing, said this:
“The ultimate vision for the digital twin is to create, test and build our equipment in a virtual environment. Only when we get it to where it performs to our requirements do we physically manufacture it. We then want that physical build to tie back to its digital twin through sensors so that the digital twin contains all the information that we could have by inspecting the physical build.”
At this point at the latest, Industry 4.0 will come to mind. We’re indeed creating a new benefit by consciously planning, programming, and enriching the digital twin of an actual object with information and making it accessible. Things and machines are equipped with sensors, actuators, and other smart components to determine applicable parameters in real-time and analyze them accordingly. Communication is bidirectional, of course, which also makes it possible to directly influence behavior and deployment scenarios.
With this development, industry sectors increasingly contribute to the growth and advancement of objects connected to the internet. As such, Industry 4.0 is driving an ever-stronger correlation between manufacturing and logistics. The real advancement will be achieved with all parties along the supply chain being able to access individually relevant information of the digital twin of a product or a resource throughout its complete lifecycle.
But this is still a future vision – to date, many supply chain parties still record their own data and run their own applications without sharing. Considering the digital twin as an overarching, standardized template and controlling access rights through this central data basis in line with relevant use-cases will make this future vision much easier to achieve.
At this point, there are many unresolved questions: missing standards for digital twins, ownership of data, and quite importantly, security around misuse and counterfeit. Complaints about missing standards around Industry 4.0 have been around for a while, and global norms are unlikely to take effect in the foreseeable future. But if every manufacturer of IoT devices was to follow the idea of the digital twin in line with certain basic principles, it would already make a big difference. At the top of the list of requirements should be well-documented application programming interfaces (APIs) for data and functionality models.
With regards to data security and control of data exchange and data access, new opportunities have come up through blockchain technology. For today, I will conclude: for now, the digital twin is neither a new development nor a revolution. But applied consistently as a model and essential component of products and services, it presents tremendous potential – especially for supply chain management. Its relevance unfolds from monitoring and control to continuous optimization and full autonomy. And in conjunction with a blockchain approach, the digital twin may indeed lead to a revolution for the collaboration within value chains and overall value chain optimization.