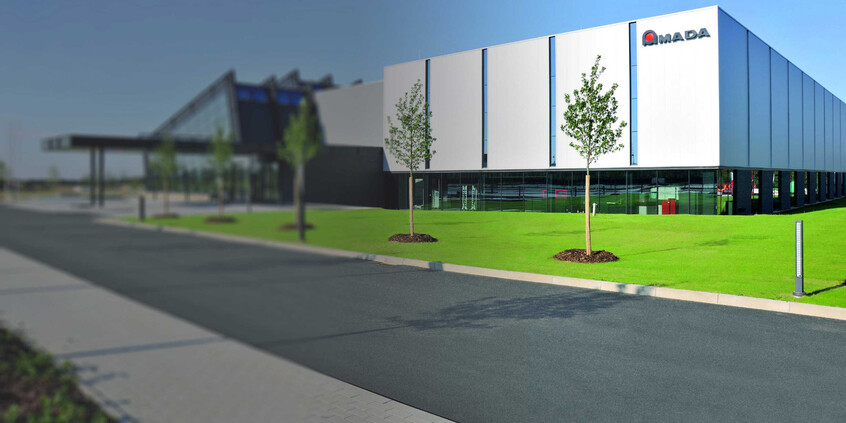
Efficient shipping: AMADA enhances quality of service
AMADA GmbH successfully manages its entire supply chain with AEB software solutions for shipping, monitoring and alerting, and freight cost control.
AMADA GmbH successfully manages its entire supply chain with AEB software solutions for shipping, monitoring and alerting, and freight cost control.
Facing logistics modernization
About AMADA
Fewer shipping steps, uniform processes, one system
Shipment monitoring and tracking for employees and customers
By truck to Kazakhstan, by air to Hungary
Collective consignment to Moscow
Freight costs: Optimized shipping invoices
Freight costs at the click of a mouse
Looking ahead: goods receipt, customs warehouse, cross-warehouse inventory management
More about AMADA: High technology in green pastures
“When it came to logistics, we used to be pretty backward. Today we are moving in the right direction – forward,” concludes Andreas Tänzer, IT Manager at AMADA GmbH.
The AMADA group is a leading manufacturer of sheet metal fabrication equipment with a complete portfolio of cutting, bending, punching, and laser technologies complemented by modular automation components, software applications, and a wide array of tools. The AMADA group was founded by Isamu Amada in Japan in 1946; its German subsidiary AMADA GmbH was founded in 1973. In 2011, the AMADA group generated revenues of US$1.98 billion.
In September 2009, AMADA GmbH opened its new company headquarters in Haan, near Düsseldorf. The 7.1-hectare site is home to the solution center with its large showroom and offices, the AMADA School for customers and employees, and the 1,500 square meter logistics center, where 13,000 articles are stored. Respect and responsibility for nature and the environment are an important part of the corporate philosophy. That’s why the AMADA site includes one of the largest geothermal facility in the state of North Rhine – Westphalia and some 4 hectares of the site are landscaped.
All shipping and exports in the Haan headquarters are managed with AEB software. Solutions from AEB’s Customs Management and Transport & Freight Management portfolio have been used since September 2011 – with very satisfying results, in the opinion of Logistics & Purchase Manager Sabine Mertens and IT Manager Andreas Tänzer.
Before, work was divided into many individual steps. IT Manager Andreas Tänzer tells of the varying processes for creating transport labels: “Forwarding orders had to be created manually, and freight charges had to be laboriously calculated and then carried over to the invoice.” The entire packing process was very time-consuming, confirms project manager Sabine Mertens.
Today, employees save time and no longer have to walk such long distances. Now the packing stations serve as centers for packing, weighing, and printing forwarder and parcel service labels and packing lists. All the data is scanned into the system, which then automatically generates the shipping documents.
Three stations in the logistics center are set up as packing stations running AEB’s Shipping software. Every evening, the loading lists are automatically transmitted to the transport service providers. If a shipment contains hazardous goods, the ADR label is printed – also automatically. The new organization in goods issue is also much more transparent.
Before, the fact that the delivery note had been printed did not automatically mean that the goods had left the warehouse. Today, all you need to do is enter the consignment number in AEB’s Shipping to see who did the picking and packing and when, whether the labels have been printed, and whether the goods have been issued. But AMADA went one step further to achieve transparency throughout the supply chain.
AEB’s Monitoring & Alerting was implemented in September 2012. Since then, all status updates are transferred to the online platform – both internal milestones such as “ready to ship” and “goods issued” as well as tracking & tracing information from the transport service providers. Logistics Manager Sabine Mertens: “The moment we promise a shipment to our customers – as soon as the order confirmation is printed – the data is passed to the visibility platform, where all subsequent steps along the supply chain can then be tracked: from packing and document printing to the arrival in the forwarder depot and receipt of the goods by the customer. The shipping status is now visible at all times.”
The sales and service personnel are the greatest beneficiaries of such transparency. Over 60 employees have access to the AEB’s Monitoring & Alerting. Sabine Penn-Destler, Sales Administration Manager: “One reason we decided to implement the online platform was so that we can respond to possible shipping delays before it is too late. This allows us to offer our customers an even higher level of service.”
Sabine Mertens describes further plans to grant access to AEB’s Monitoring & Alerting to customers that have obtained partner status or signed special service agreements. “At the beginning of 2013, these customers will even be able to check the shipping status on their own.”
But the sales staff already has direct access to this information and no longer has to go to the trouble of requesting the shipping status or checking the websites of the transport service providers. “We expect the administrative workload in our sales and service departments to shrink significantly,” says Penn-Destler.
The portal also makes it possible to evaluate the on-time performance of parcel services – for example, by tracking whether “next day by 9:00 a.m.” delivery guarantees were actually kept.
Sabine Mertens describes the benefits of the online solution: “We will use the solution to monitor our delivery times internally and calculate lead times forward and backward. Alert levels have been defined in case a milestone is not reached on time. This way, we make sure we pick early and are able to give the customer reliable information at any time.”
Some 108,000 replacement parts and accessories are shipped each year from Haan. This represents between 17,000 and 25,000 shipments or 30,000 packages. Some 70 shipments leave the spare parts warehouse in Haan each day. Some 25% goes out to other EU countries and 3% to non-EU countries, especially Russia. The carriers use trucks for shipments as far away as Kazakhstan. The Moscow subsidiary also receives a collective consignment once a week. All shipping and export documents are generated at the Haan headquarters, even if the shipments themselves go out from the external logistics centers.
Sabine Mertens: “All the shipping data goes through AEB’s Shipping, even for shipments that are not processed at the packing stations. We make no exceptions – not even for those who pick up their own goods. AEB’s Shipping now keeps track of every single shipment.” Mertens sums it up this way: “With AEB’s solutions, we have made end-to-end processes, visibility, and transparency a reality. ”The introduction of the software suite even paid off in day-to-day operations, as the following examples illustrate.
Another way to save time, according to Sabine Mertens, comes from using AEB’s Shipping to create collective consignments. Today, export consignments are handled like domestic shipments. As soon as an order from Russia is received, the system opens a collective consignment. The warehouse staff can process the packages one by one and affix a neutral label.
Each individual package is assigned the status of “packed” in AEB’s Shipping. One day before the pickup date, all the packages undergo qualified packing as a collective consignment based on the delivery note list. The boxes are packaged together, and the export administrator adds the appropriate export documents.
“Before, we had to manually assign documents to outbound goods. Creating an invoice for outbound shipments was very time-consuming and labor-intensive,” explains Logistics Manager Mertens. Since January 2012, all carrier contracts have been saved to AEB’s Freight Cost Management, and since April 2012, the freight costs and tracking & tracing numbers have been fed back into the ERP system.
All this information is needed to create invoices for outbound shipments. The automatic transmission of the freight costs calculated by AEB’s Freight Cost Management saves each of the nine employees about 20 minutes a day – a tremendous time gain over the course of the year, says Mertens.
The Logistics Manager is glad that she is now able to quickly let controlling know the amount of anticipated freight costs. “Our freight costs can be very expensive, especially for our machinery, which often requires multiple truck transports. That’s why we set aside reserves for our freight costs. Before, I couldn’t say exactly how high our pending transport costs were.
Now, I press a button and have an answer to pass along to my colleagues from controlling.” This also makes invoice auditing much easier: “Before, we had piles of paper invoices and could only roughly estimate whether the amounts were correct. Today, you can enter the billing period in AEB’s Freight Cost Management and immediately see the total freight costs.”
Optimized supply chain processes from procurement to fulfillment with AEB's supply chain and logistics software. Including monitoring and alerting, carrier integration, shipping processes, freight and logistics cost management, and warehouse management at the heart of global distribution centers.
When it comes to providing customers with replacement parts, the enhanced transparency of AEB’s Supply Chain Collaboration platform means better service. A problem with one of the machines was always reported quickly. Today, as soon as an order is received, all shipping and supply activities are trackable online and can be monitored. Sabine Mertens continues to focus on improving processes. She still sees potential for optimization in warehouse management and customs clearance.
And an inventory management system that links all storage facilities is another vision she has for the future. “A standardized platform offering visibility of all inventory in all storage sites across Europe would benefit AMADA greatly. With the click of a mouse, we could see where a particular replacement part is in stock.” The AEB solution has already successfully turned this vision into reality in other enterprises.
Those who visit the headquarters of AMADA GmbH experience a symbiosis of nature and high-tech. The approach takes you along a vast open space with a landscaped lawn dotted with bushes, rows of cherry trees, and a leafy orchard. In the midst of this greenbelt lies the architecturally striking AMADA solution center: Oblique glass facades accentuated by black beams, an artificial lake – and last but not least, the airy, light-filled reception area that welcomes visitors into a friendly ambience of natural stone.
The solution center is a place where AMADA puts its values into practice: appreciation for the customer, respect for the environment, and innovative technology. The showroom, covering more than 2,000 square meters, introduces visitors to the forward-looking, custom product solutions offered by AMADA’s broad product portfolio.