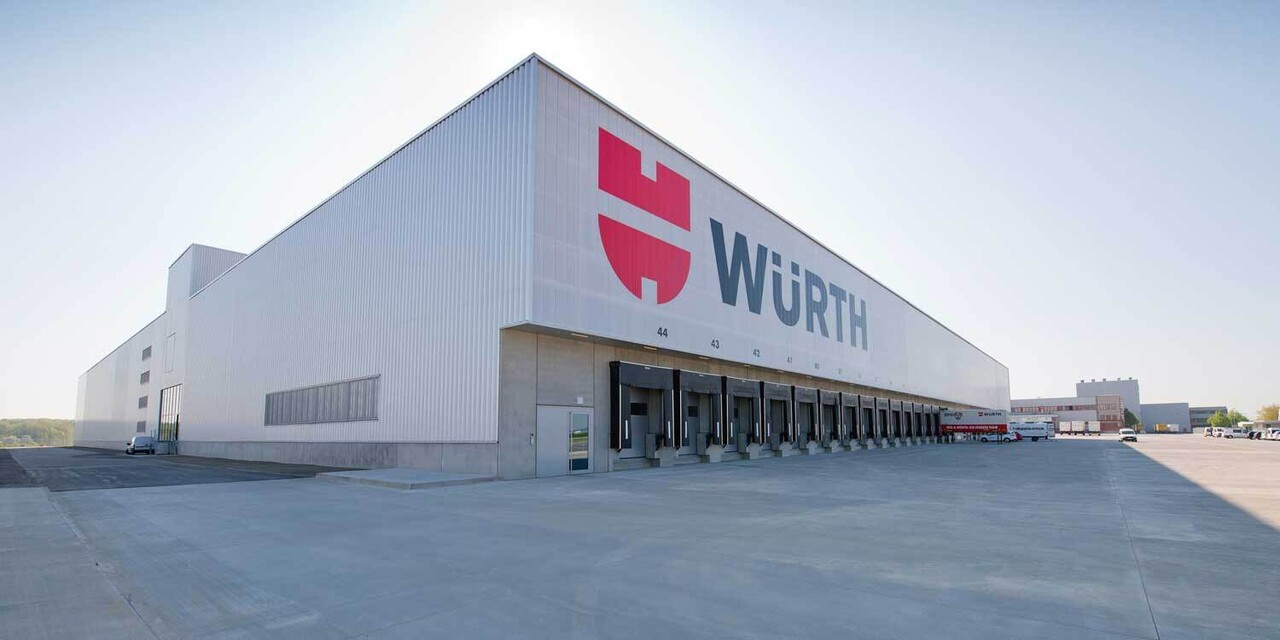
Supply chain event management: Visibility in fulfillment
Adolf Würth GmbH & Co. KG is breaking new ground in supply chain event management through enhanced visibility across its shipping process – thanks to monitoring software from AEB SE.
Adolf Würth GmbH & Co. KG is breaking new ground in supply chain event management through enhanced visibility across its shipping process – thanks to monitoring software from AEB SE.
Fulfill the unique needs of every customer with the assembly and fastening materials they need: That’s the mission of Adolf Würth GmbH & Co KG. Würth’s logistics team ships some 40,000 packages and 1,500 pallets from over 20 shipping points each day – handling 125,000+ articles and serving more than 540,000 customers, from independent contractors to regional construction companies to global industrial enterprises. That creates quite a challenge for the company’s supply chain event management.
Würth, based in the southern German town of Künzelsau, relies on a mix of direct sales, e-commerce, and brick-and-mortar retail. Over 530 sales outlets throughout Germany serve the immediate needs of customers with an inventory of 5,000 to 6,000 different articles.
Customers with an urgent need for a part at a construction site or on the shop floor can call on Würth’s express service, which will dispatch a courier to deliver any article from the core product line within three hours from the company’s network of sales outlets, which function as “regional mini-warehouses” for customers.
The company’s logistics services and processes have proven their worth over the years, receiving the coveted German Award for Supply Chain Management in 2009. But Würth is always working on optimizing its processes, of course, as with its extensive “Order and Transport Control” project launched in 2016. “We wanted to further optimize the range of fluctuation in our supply chain performance and make our services even more predictable for our customers,” explains Mino Broselge, Director of Fulfillment Logistics at Würth. Even though the quality of shipping services was good overall, it sometimes happened that multiple shipments of a single order would arrive at different times, on different days, or with different transport providers. That makes the quest for better supply chain event management essential.
The overriding objective of the mammoth project: to improve customer service. “We wanted to bring about a paradigm shift in fulfillment,” says Dirk Antrack, Director of Information Management for Logistics at Würth. Instead of fulfilling customer orders with a productivity-oriented approach, Würth wanted its customer interactions to be defined by openness, reliability, and transparency. This would be a plus for supply chain event management as a whole.
Würth responded by changing its procedure for dispatching, processing, and completing shipments. “The time of delivery to the customer became the defining event,” Antrack explains. The shift in focus created ripple effects across the entire fulfillment process, which is now aligned with the loading times of transport service providers. This led to a complete redesign of 15 processing steps, from the initial purchase order to delivery to the end customer.
Würth uses a monitoring system from Stuttgart-based software provider AEB to continuously improve how orders and shipments are dispatched and managed. This helps the logistics team at the tactical and strategic level. The goal: Analyze the supply chain performance and identify any potential for optimization in the overall process or in individual steps in the process.
The software defines the individual steps in the fulfillment process as milestones and assigns target times, which are stored in Würth’s SAP® system. It also collects data on actual times – for example, from Würth’s ERP and warehouse management system and from the transport service providers. The AEB system compares these actual times to the defined target times. This allows the software to highlight which steps are creating delays when, where, and how often, and where bottlenecks are occurring.
Würth went live with the AEB monitoring system in 2018. “Since then, we’ve made tremendous strides in visibility,” Mino Broselge is happy to report. Würth has also cultivated a different mindset – not only in management, but also at the team leader level. In-house logistics teams now look beyond the productivity of their own sphere and focus on ensuring that customers receive their shipments when promised. This provides comprehensive monitoring of the supply chain event management.
In order dispatching and processing, the system ensures that loading rates are maintained at the shipping point level and generates corresponding daily reports. “The AEB solution helps us assess how well we’re keeping our commitments to customers and where there is still potential for optimization,” Broselge finds. The monitoring system also brings extra visibility of transport service providers by making it possible to evaluate their transit and delivery times, which helps identify weak points. If, for example, a consignment leaves Würth’s logistics on time but still arrives late at the customer site, the wholesaler can explicitly ask the service provider and work together to solve the problem.
“We wanted to identify problem areas with the aim of streamlining process optimization,” says Broselge, “and thanks to AEB’s monitoring system, we succeeded.” But the happiest people are those at the end of the supply chain, those who are always the focus at Würth: the customers. “Our enhanced on-time performance shows us how the quality of our logistics has improved and how stable and reliable our shipping has become,” he adds, praising the supply chain event management.
Optimized supply chain processes from procurement to fulfillment with AEB's supply chain and logistics software. Including monitoring and alerting, carrier integration, shipping processes, freight and logistics cost management, and warehouse management at the heart of global distribution centers.
Even though the project is actually complete, Würth continues to discover more and more benefits of AEB’s monitoring system – most recently, for example, when it comes to big data: “We’re in the process of launching a huge statistical system. We transfer data received from the AEB software to our SAP® BI statistical system, where it is linked to sales data,” explains Dirk Antrack. By linking logistics and sales data, Würth hopes to eventually generate even more detailed analyses of supply chain performance at the customer and industry level. This would further benefit the entire supply chain event management. Mino Broselge and Dirk Antrack are of one mind in summarizing their experience with the AEB software: “We’ve achieved complete visibility across the entire shipping process, allowing us to pinpoint our ongoing process optimizations.”
Würth brought Stuttgart-based AEB on board early on. “We did approach other providers, but we quickly decided to go with the AEB solution,” recalls Dirk Antrack, the responsible project manager at Würth. The fact that many other companies were already working successfully with AEB was yet another selling point.
It wasn’t so simple nailing down the functional specs, however, since the new monitoring system was to be just one of seven components in Würth’s mammoth project. That’s why this phase took more time than usual.
“But the in-depth discussions with AEB yielded various insights that helped our other projects,” notes Antrack with satisfaction. He has nothing but praise for the working relationship with the software company: “AEB kept drilling down to find out exactly what we want at Würth, what we stand for, and what business processes are behind it.” Mino Broselge echoes this praise: “The discussions were always focused on the goal of offering us a perfectly tailored monitoring solution.”
The AEB software also offers features that let you monitor and better control the operational processes. The software helps answer such typical questions as: Will unpacked goods lead to negative downstream effects such as a missed delivery date? Could a courier or parcel service deliver the shipment faster than the scheduled carrier? Or will the carrier get the job done on time after all, even if it doesn’t receive the consignment until the next day? If the delivery will indeed be late, the software can automatically notify the appropriate person, such as a customer support agent, who in turn can give the customer a heads-up.
The AEB solution also offers features for workload monitoring. This helps shipping points stay constantly abreast of the pending workload for each step in the intralogistics process throughout the workday. Workload monitoring can also visualize the workload of a dedicated step in the process – such as picking – on an hour-by-hour basis. This enables the cross-functional management of resources in operations based on both the planned and actual workload.
The AEB system can generate package forecast data for each workday based on current actual and past figures to help transport service providers manage their capacities. Forecasting data can be queried by parameters such as carrier, shipping point, or package type. The predicted transport volume of the carriers can also be broken down to the postal code level. This makes it possible to better estimate the expected volume per transport service provider and, for example, to request an additional swap body early on if the volume to a particular region is unexpectedly high.
Monitoring & Proactive Alerting | Workload Monitoring | Capacity Forecasting |
---|---|---|
Continuous comparison of target times to actual times for each process step | Overview of workload completed for each process step | Package forecasting data for each workday |
Automatic alerts of critical delays | Overview of workload pending for each process step | Query by criteria such as carrier, shipping point, or package type |
Visibility of order and shipping status across entire process chain | Workload per intralogistics process step on hour-by-hour basis | Forecast of volume by carrier down to postal code level |