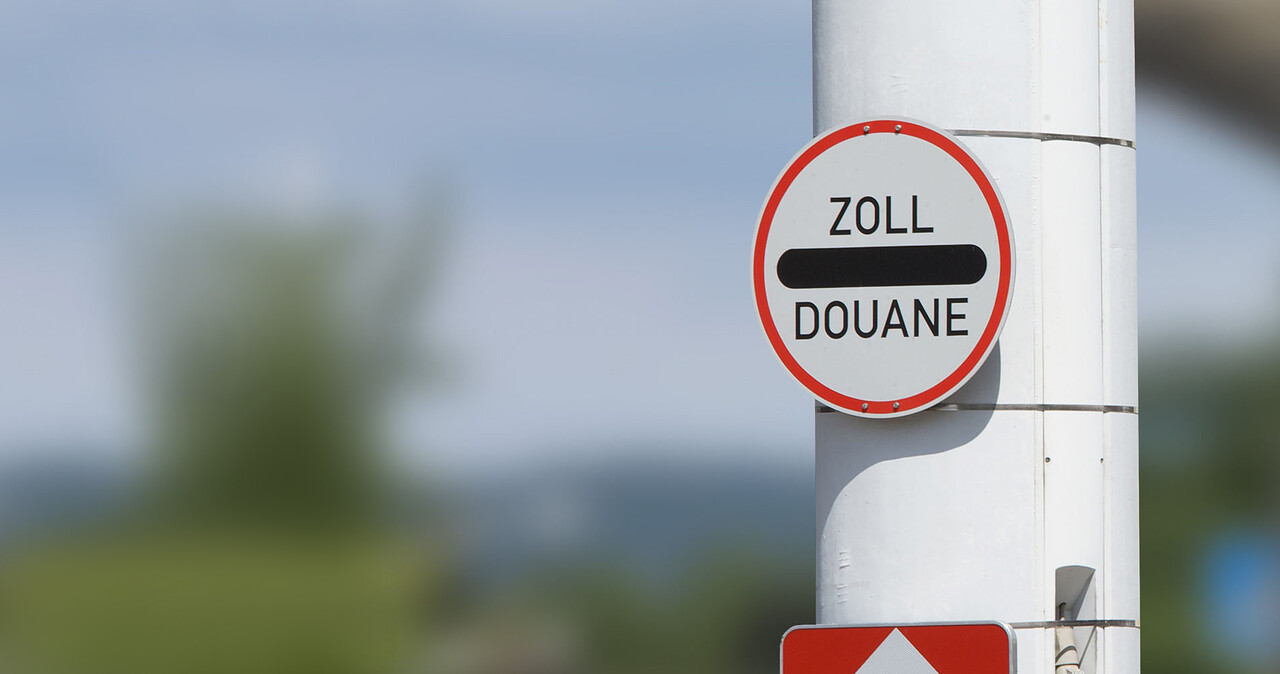
Customs processes in spare parts management
Speed is of the essence in spare parts management. How can suppliers manage customs processes to their advantage to gain a competitive edge? Tangible tips.
Speed is of the essence in spare parts management. How can suppliers manage customs processes to their advantage to gain a competitive edge? Tangible tips.
Idle machines are the worst nightmare for any manufacturer. The damage this brings is often immeasurable. Quick action is needed. The defective part must be replaced – immediately.
This puts pressure on the spare parts supplier to respond quickly and deliver ASAP. It’s critical that supply chain processes run smoothly – especially across international borders – so that the supplier can ship the right part to the right place at the right time.
Despite preventative maintenance management, manufacturers still need to be prepared for an equipment failure. It’s essential that they obtain complete and accurate information on the necessary replacement part so that the shipping process goes smoothly.
If the customer is unable to identify the defective part with certainty, it may be necessary to send a service technician to the site to assess the situation and provide the missing information. This takes time and delays the repair work.
That’s why any optimization measures depend on spare parts being clearly identifiable to all parties. It helps if spare parts suppliers know as much as possible about the equipment types, locations, and maintenance processes of their customers. Ideally, this allows them to even diagnose remotely which part is likely defective.
The only way to truly be a good supplier is to understand the business and workflows of your customers. Experts recommend establishing clearly defined service levels right from the onset. This way customers and suppliers both know exactly what is expected of them. And spare parts suppliers need to optimize their own inventory and warehouse management, of course, to avoid running out of stock and to ensure quick deliveries.
It’s important to take upstream procurement processes into account as well. Spare parts suppliers need to know exactly which parts can be obtained how quickly and with what lead times. If customers have been promised rapid response times – 12 or 24 hours, for example – the necessary parts may need to be back-stocked in sufficient quantity.
Equipment makers who don’t wish to keep their own emergency parts inventories can also turn to service providers or partnerships among spare parts distributors. This type of partnership is often critical in long supply chains or those across international borders. As a result, it’s not always so important to have the necessary part in your own warehouse – you just need know which one of your partners has it in stock.
Customs management plays a critical role when customers are outside the EU or when the required parts must be procured outside the EU. Traditionally perceived as somewhat of a burden, this area is complex but can be well managed to the advantage of a business:
With the right information at the right time and the right customs procedures, it’s possible to accelerate processes and even save customs duties at the same time. Global trade management as an element of supply chain management is a critical tool to achieve time gains and use customs procedures strategically to minimize customs and import duties. When it is done right…
Businesses with foreign customers are typically in good shape when it comes to exports. When they receive orders for exports, they generally think right away about how they can get any spare parts across borders to their customers without delay.
Having the right IT support is always a key factor. From warehouse and inventory management to shipping and the transmission of shipping information to the carriers: software helps render supply chain processes clear and transparent. Even – and especially – between different customs areas.
IT has also become an indispensable ingredient of well-functioning partnerships in the spare parts sector. Experts agree on this: from the customers to the suppliers and beyond to the business partners and manufacturers – a seamless chain of communication must be in place.
How you do manage your spare parts supply chain? Which customs procedures do you take advantage of and how integrated are all involved parties and processes? Just contact us to discuss your logistics, compliance, and customs software requirements to optimize your processes.